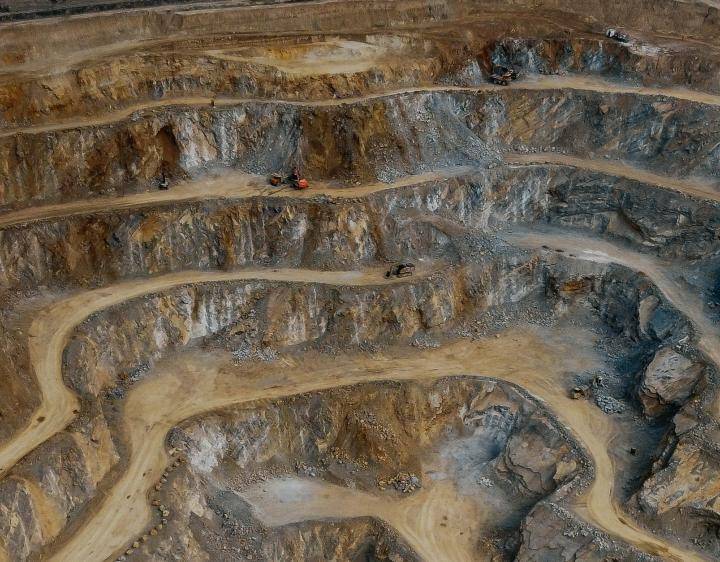
Rare earth elements have long been the quiet enablers of modern technology, essential to everything from clean energy to medical imaging and defence systems. But as geopolitical tensions rise, these materials are no longer just industrial inputs; they’ve become strategic assets in the global race for supply chain resilience. And one country has dominated for over two decades: China.
Estimates put China’s share of rare earth processing upwards of 90%1, a critical point in global supply chains. For companies and countries alike, reducing this dependency has become an economic and security imperative. Rare earths are now a key chip in global power plays.
So, what exactly are rare earths?
They are a group of 17 metals, that possess unique magnetic, thermal, and chemical properties. Some, like neodymium and praseodymium, are alloyed with iron and boron to create permanent magnets, indispensable for high-performance electric motors and wind turbines. Small amounts of heavy rare earths, including dysprosium and terbium, are often added to improve temperature resistance, crucial for electric vehicle (EV) applications. The name ‘rare’ can be misleading; rare earths are ironically relatively abundant, instead it is their dispersion and lack of concentrated deposits that make them ‘rare’. This is what makes extraction and refining costly and complex making China’s dominant position so important.
The rare earth story didn’t actually start in China
The United States, anchored by California’s Mountain Pass mine, once led the market. But lower costs, higher subsidies and looser environmental regulations enabled China to scale production and invest heavily in refining, capturing a near-monopoly in the early 2000s. The fragility of this position became evident in 2010, when China temporarily halted rare earth exports to Japan during a territorial dispute, triggering a global wake-up call.
In response, Japan diversified supply sources, invested in recycling, and accelerated technologies to reduce rare earth use. Japanese manufacturers have since cut their dependence on Chinese rare earths by a third, and overall consumption has fallen by nearly 50%2. Today, similar strategies are being adopted globally as governments and industries seek to build more resilient, sustainable supply chains.
Wind turbines and electric vehicles are key consumers of rare earths
Many modern turbines, particularly for offshore wind, use a direct-drive (gearless) systems that rely heavily on rare earth permanent magnets. A single turbine alone can contain up to five tonnes of magnets, with rare earths accounting for roughly 30% of that weight3. This exposes manufacturers to supply chain volatility and rising material costs.
Corporations are adapting. Vestas, the world’s leading wind turbine manufacturer and a WHEB portfolio company, has actively reduced its reliance on rare earths with its EnVentus platform4. Its modular designed geared turbine uses up to ten times fewer rare earth materials than direct-drive designs. This engineering choice reduces exposure to critical raw materials, while maintaining strong efficiency and serviceability. Demonstrating that sustainability and innovation can be mutually reinforcing.
In the Electric Vehicle (EV) sector, there are still considerable trade-offs in efficiency, weight, and cost, but alternative motor technologies that reduce or eliminate rare earths are slowly emerging.
The future of rare earths - primary supply and scalable recycling
Even with technological breakthroughs to lower dependency, global demand for rare earth magnets is set to surge. The International Energy Agency (IEA) projects[5] that wind turbines alone could account for as much as 60% of rare earth magnet demand in ambitious net-zero scenarios, with EVs adding further pressure.
This makes recycling – dubbed as “urban mining” - critical. Secondary supply from end-of-life equipment, offers a pathway to easing resource bottlenecks.
The IEA forecasts6 that by 2030, magnets from retired wind turbines and EV motors will enter the recycling stream. By 2040, these sources could account for 15% of all end-of-life magnets, rising to nearly 25% in EVs and 50% for wind turbines by 2050 under current policy trends. Whilst consumer electronics offer some opportunity, recovery rates remain below 5%, and the high concentrations of rare earths in the magnets of wind turbines and EV motors are much easier to access.
Momentum is building across the industry. Recycling projects have been announced across Canada, China, France, Germany, the UK, and the US, targeting both manufacturing scrap and end-of-life magnets. Publicly disclosed projects represent around 30,000 tonnes of waste processing capacity annually, containing approximately 8,000 tonnes of rare earths, equivalent to around 7% of forecast demand by 20267.
Even with this secondary supply from recycling, magnet demand will remain elevated for decades, reinforcing the need for both primary supply and scalable recycling. The unavoidable conclusion is that recycling will not replace the need for new mining, but it can reduce dependence on primary extraction, mitigate geopolitical risks, and support a circular economy.
The rare earth landscape presents both challenge and opportunity and will remain central to the green economy. Companies innovating in material efficiency, recycling technologies, and supply chain diversification are well-positioned to benefit from the global transition to net zero. The most compelling story is how industries are learning to do more with less, turning scarcity into a catalyst for innovation.
Sign up here to receive our monthly and quarterly commentaries in your inbox.
1 https://www.iea.org/reports/global-critical-minerals-outlook-2024
2 https://www.weforum.org/stories/2023/10/japan-rare-earth-minerals/
3 Quoted from Adamas Intelligence: https://givingcompass.org/article/challenges-around-rare-metals-powering-wind-energy
4 https://www.vestas.com/en/energy-solutions/onshore-wind-turbines/enventus-platform
5 https://www.iea.org/reports/recycling-of-critical-minerals/executive-summary
6 https://www.iea.org/reports/recycling-of-critical-minerals/executive-summary
7 https://www.iea.org/reports/recycling-of-critical-minerals/executive-summary